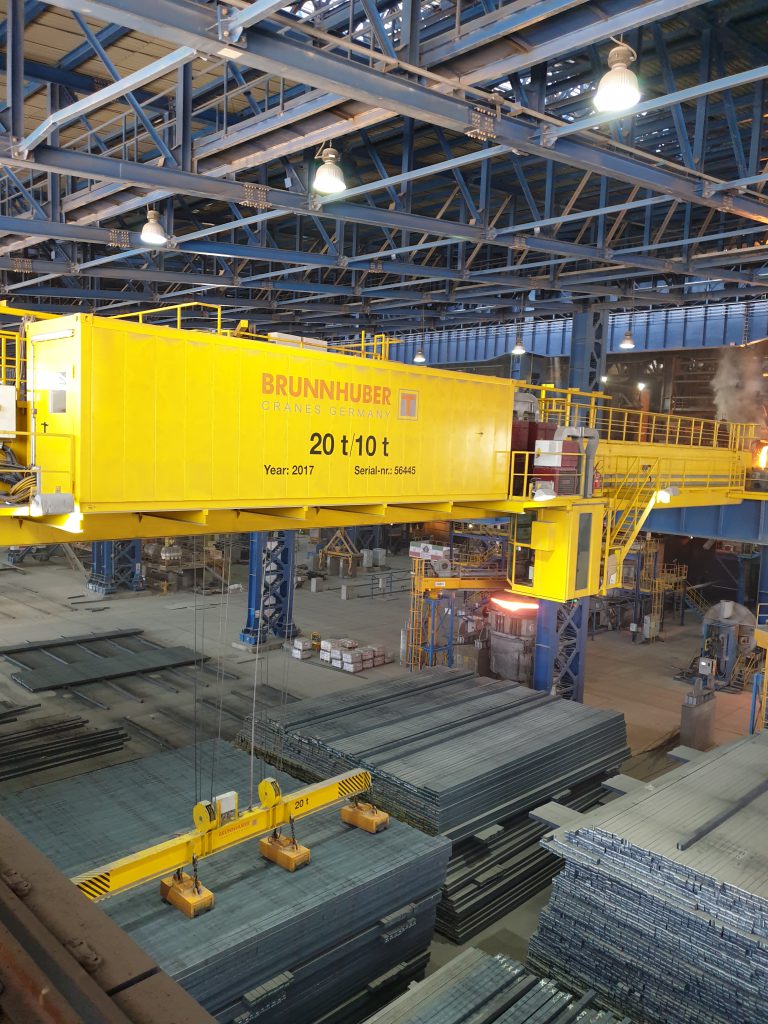
The project team’s tasks include consultation, design, programming, installation, and implementation of automation control systems as well as reconstruction of the production process control system using precise tools. In addition, the team is responsible for quality control and safety.
Here are some records of the project team:
– Supply, installation, and commissioning of the engine and drive of the Kokil machine (pipe casting)
– Supply, installation, and programming of PLC and HMI for the washer-filler device of purified water
– Supply, installation, and operation of the temperature controller and related sensors in the oxygen plant
– Designing, supplying, and assembling the automatic transfer system of the bus section of power plant units
– Investigating and fixing the problems of the steel crane system and providing the required equipment
– Design and installation of the router system using laser sensors for the pipe testing machine
– Designing the fluid level control system in the reservoirs at the request of the water supply company
– Designing and manufacturing the control system of the rolling mill
– Designing, providing equipment, and making signs for the main pumping station
– Designing, providing equipment, and installing the record and alarm system of the temperature sensors of the main rolling process engines
– Design, equipment supply, and installation of record and alarm system for temperature protection of circulating water pumps (CWP) in power plant
– Design, supply, and construction of signs for the sewage pumping station
– Design, supply, and manufacture of water pumping station panels
– Changing the air heater system of the power plant from DC motor to AC motor and controlling them redundantly
– Designing a set of electrical systems and instrumentation and whistleblower control of power plant
– Design and implementation of the electrical system and precision instruments of the hydro test group
– Design and construction of the exhaust fan starting system of the Ferrochrome factory
– Updating the electricity and control system of petrochemical packaging lines
– Redesign, installation, and commissioning of busbar switches for internal consumption of the power plant (315 MW)
– Design and implementation of the automation system and precision instruments of the furnace and piping line
– Installation and commissioning of electrical systems, instrumentation, and control of paper factory
– Design and construction of the electrical panel of the chemical warehouse project
– Providing drives of 200 kW and 315 kW HDPE units of the Petrochemical Company
– Designing and manufacturing the main incoming switchboard for the extruder line of Dynamic Polymer Mixtures Company
– Design, construction, and commissioning of the electrical system and control of the stone paper production line
– Supply of ABB brand DU/DT filters for 200 kW petrochemical drive
– Redesigning and implementation of electrical system, precision instruments, and control of roll grinder machine in the steel complex